Steel is one of the most versatile and widely used materials in construction, manufacturing, automotive, and various other industries. Among its many forms, hot rolled and cold rolled steel are two of the most common types, each with unique properties and applications. This guide explains the fundamental differences between hot rolled and cold rolled steel, their specifications, and the advantages and disadvantages of each to help you make an informed choice.
What is Hot Rolled Steel?
Hot rolled steel is steel that has been heated above its recrystallization temperature (around 1,700°F or 926°C) and then rolled into a desired shape. This high-temperature process makes the steel more malleable, enabling it to be formed into large and intricate shapes easily. Hot rolled steel is commonly used in situations where precise shapes and tolerances are not critical.
Specifications Table for Hot Rolled Steel
Property | Specification |
---|---|
Surface Finish | Rough and slightly scaly |
Tolerances | Less precise; more dimensional variability |
Thickness Range | 1.5mm to 20mm+ |
Yield Strength | Lower due to high-temperature processing |
Applications | Structural beams, railroad tracks, sheet metal |
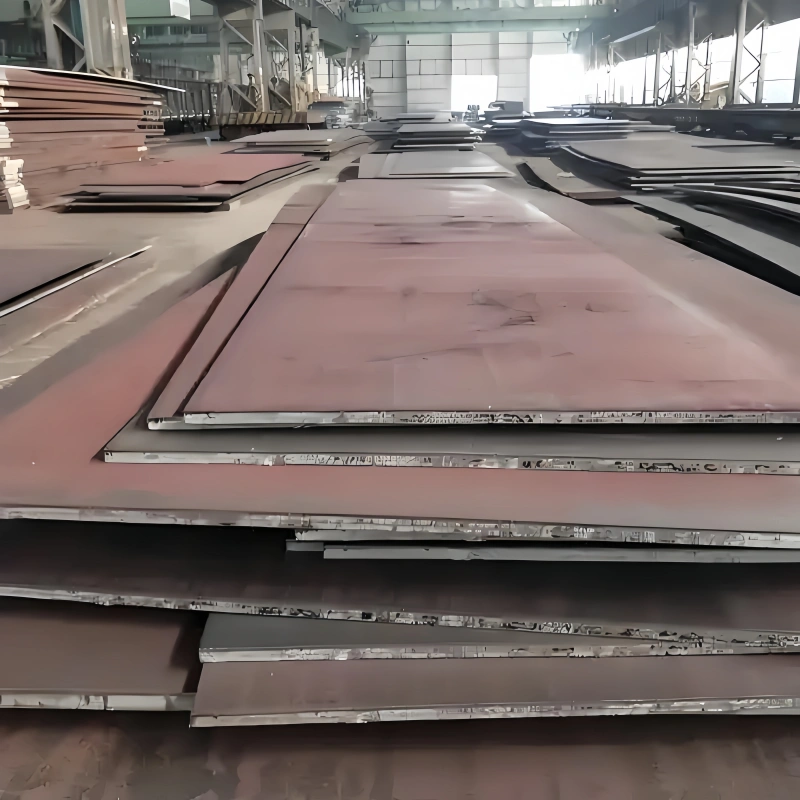
What is Cold Rolled Steel?
Cold rolled steel starts as hot rolled steel, which is then further processed at room temperature to refine its shape and dimensions. Cold rolling enhances the strength and surface finish, making it ideal for applications that require precise tolerances and a smooth surface. Cold rolled steel is commonly used in consumer goods, automotive parts, and precision equipment.
Specifications Table for Cold Rolled Steel
Property | Specification |
---|---|
Surface Finish | Smooth and often shiny |
Tolerances | More precise; tight dimensional tolerances |
Thickness Range | Typically under 3mm |
Yield Strength | Higher due to work hardening |
Applications | Automotive parts, home appliances, furniture |
Differences Between Hot Rolled and Cold Rolled Steel
Characteristic | Hot Rolled Steel | Cold Rolled Steel |
---|---|---|
Processing Temperature | Above recrystallization (around 1,700°F) | Room temperature |
Surface Finish | Rough, scaly | Smooth, often shiny |
Dimensional Accuracy | Lower accuracy, more variability | High accuracy, tight tolerances |
Strength | Lower due to high temperature | Higher due to work hardening |
Cost | Generally cheaper | More expensive due to additional processing |
Applications | Structural work, large shapes | Precision parts, consumer goods |
1. Cold-rolled steel allows local buckling of the cross section, so that the bearing capacity of the bar after buckling can be fully utilized; while hot-rolled steel does not allow local buckling of the cross section.
2. The causes of residual stress in hot-rolled steel and cold-rolled steel are different, so the distribution on the cross section is also very different. The residual stress distribution on the cross section of cold-bent thin-walled steel is bending type, while the residual stress distribution on the cross section of hot-rolled steel or welded steel is film type.
3. The free torsional stiffness of hot-rolled steel is higher than that of cold-rolled steel, so the torsional performance of hot-rolled steel is better than that of cold-rolled steel.
Pros and Cons of Hot Rolled Steel
Pros
Lower Cost: Hot rolled steel is generally more affordable due to the simplified high-temperature processing. There’s no need for post-rolling cooling, making it less costly to produce.
Malleability: High-temperature processing makes the steel more pliable, enabling it to be easily formed into larger and more intricate shapes.
Suitable for Structural Applications: Hot rolled steel is ideal for applications where exact dimensions and finishes are not critical, such as beams, rails, and metal frames.
Cons
Less Precise Tolerances: Hot rolling doesn’t provide tight dimensional accuracy, leading to more variability in thickness and shape.
Rough Surface Finish: The steel has a rough, scaly surface that might need additional processing for certain applications.
Lower Strength: Due to high-temperature processing, the yield strength of hot rolled steel is lower than that of cold rolled steel.
Applications of Hot Rolled Steel
Construction and Structural Components: Hot rolled steel is often used in I-beams, H-beams, rails, and large structural sections.
Railroad Tracks: Its malleability and lower cost make it suitable for large infrastructure applications.
Sheet Metal and Heavy-Duty Machinery: Hot rolled steel is common in machinery and other applications where high strength is required but surface finish is not critical.
Pros and Cons of Cold Rolled Steel
Pros
High Dimensional Accuracy: Cold rolling allows for tighter tolerances, making it ideal for applications that require precision.
Smooth Surface Finish: The cold rolling process gives the steel a smooth, sometimes polished surface, eliminating the need for additional finishing.
Increased Strength: Cold rolled steel is stronger than hot rolled steel due to the work-hardening process that occurs during rolling at room temperature.
Cons
Higher Cost: Cold rolled steel requires additional processing, making it more expensive than hot rolled steel.
Limited Thickness Range: Cold rolling is generally limited to thinner materials; it’s challenging to produce thicker cold rolled sheets.
Less Malleable: Cold rolled steel is harder and less malleable, making it more challenging to shape into complex forms compared to hot rolled steel.
Applications of Cold Rolled Steel
Automotive and Appliance Manufacturing: Used for parts that require smooth finishes, such as car bodies, appliances, and furniture.
Precision Parts: Due to its high accuracy and strength, cold rolled steel is commonly used in precision machinery and instruments.
Consumer Goods: Cold rolled steel is preferred for items like filing cabinets, desks, and home appliances where appearance and surface quality are important.
Choosing Between Hot Rolled and Cold Rolled Steel
When deciding between hot rolled and cold rolled steel, it’s essential to consider the specific requirements of your project, including cost, strength, appearance, and dimensional accuracy. Here’s a breakdown to help guide the decision:
For Projects with Flexible Tolerances and a Need for Cost Savings:
Hot rolled steel is typically the better choice for large structural components and applications where precision isn’t crucial. If you need strength and malleability without worrying about an exact shape or a polished finish, hot rolled steel is a cost-effective option.For Projects that Require High Precision and Surface Quality:
Cold rolled steel is ideal for projects requiring tight tolerances and a smooth finish, such as parts for the automotive or appliance industry. Cold rolled steel’s increased strength and refined appearance make it suitable for visible or decorative applications.For Structural Applications:
If the steel is being used for structural purposes, consider the environment and load requirements. Hot rolled steel may be sufficient for heavy-duty infrastructure, while cold rolled steel may be necessary for more refined structural applications that require accuracy.
Summary
Criteria | Best Choice |
---|---|
Cost Efficiency | Hot Rolled Steel |
Surface Finish | Cold Rolled Steel |
Dimensional Precision | Cold Rolled Steel |
Strength | Cold Rolled Steel |
Large Structural Applications | Hot Rolled Steel |
Conclusion
Understanding the differences between hot rolled and cold rolled steel is essential for making the right choice for your project. Hot rolled steel, with its affordability and malleability, is perfect for structural components and heavy-duty applications. Cold rolled steel, on the other hand, provides a polished finish, higher strength, and dimensional accuracy, making it ideal for precision applications.
Selecting the right steel type can impact not only the project’s budget but also the performance, durability, and aesthetics of the final product. For general structural applications, hot rolled steel provides a practical solution, whereas cold rolled steel is more suited to applications requiring a refined finish and exact dimensions.
By understanding these core differences, you can make a professional and informed decision, ensuring the steel you choose meets the specific requirements of your project.